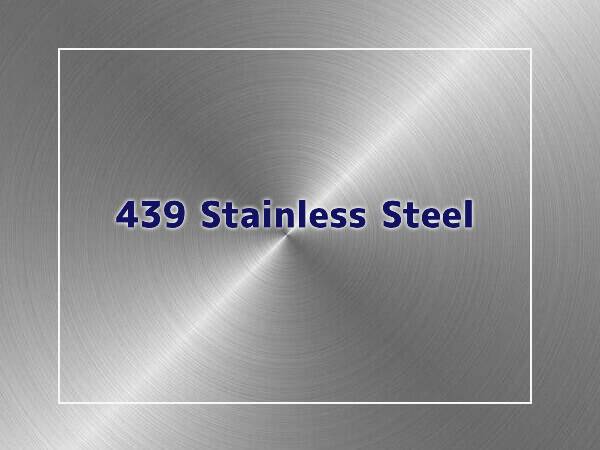
430 Stainless Steel is a classic 16% chromium ferritic stainless steel grade, a commonly used ferritic stainless steel grade with corrosion resistance approaching that of 304 and 304L stainless steel. This grade does not work harden rapidly and can be formed using both mild stretch forming, bending, or drawing operations. This grade is used in a variety of interior and exterior cosmetic applications where corrosion resistance is more important than strength. Type 430 has poor weldability compared to most stainless steels due to the higher carbon content and lack of stabilizing elements for this grade, which requires post-weld heat treatment to restore corrosion resistance and ductility. Stabilized grades such as Type 439 and 441 should be considered for welded ferritic stainless steel applications.
Stainless steel grade 430 is a non-hardenable steel containing straight chromium and belongs to the ferritic group of steels. This steel is known for its good corrosion resistance and formability, coupled with practical mechanical properties. It can be used in certain chemical applications due to its resistance to nitric acid.
430 stainless steel is an excellent lower-cost alternative to the 304 grade for those mild corrosive environments. The corrosion resistance of stainless steel 430 is close to that of stainless steel that contains nickel.
430 Stainless Steel is a very widely used ferritic, non-hardenable, stainless steel 430 has good mechanical properties that combine good corrosion resistance as well as heat and oxidation resistance up to 1500°F. When 430 is highly polished or in a buffed condition it exhibits maximum corrosion resistance. For all ferritic grades stress corrosion cracking resistance is quite high, 430 included. This grade is also easily formable which paves the way for usage in a large amount of applications as listed below. Machining 430 is easier than 304 or other austenitic grades. Drawn bars are also more easily machined than annealed.
430 Stainless Steel Chemical Composition
430 stainless steel has high chromium but very low nickel content. Chromium content is between 16 and 18%, while nickel content is 0.5% max. Its other constituents are present in trace amounts. There’s a maximum of 1% each of manganese and silicon, 0.12% carbon, and 0.03% and 0.04% respectively for sulfur and phosphorous. As before, the balance is made up of iron, around 80%.
Grade | C | Si | Mn | P | S | Cr | Ni | Fe |
---|---|---|---|---|---|---|---|---|
430 | 0.12 | 1.00 | 1.00 | 0.04 | 0.02 | 16.00 – 18.00 | 0.5 | Bal |
TP430 | 0.12 | 1.00 | 1.00 | 0.04 | 0.03 | 16.00 – 18.00 | … | Bal |
Max, %, 430 for ASTM A240 Plate, Sheet and Strip, TP430 for ASTM A268 seamless and welded tube
430 Stainless Steel Mechanical Properties
Grade | Tensile Strength (MPa) Min | Yield Strength 0.2% Proof (MPa) Min | Elongation (% In 50mm) Min | Hardness Rockwell B (HR B) Max | Hardness Brinell (HB) Max |
---|---|---|---|---|---|
430 | 483 | 310 | 22 | 85 | 183 |
TP430 | 415 | 240 | 20 | 90 | 190 |
430 for ASTM A240 Plate, Sheet and Strip, TP430 for ASTM A268 seamless and welded tube
430 Stainless Steel Physical Properties
Grade | Density (Kg/M3) | Elastic Modulus (GPa) | Mean Coefficient Of Thermal Expansion (Μm/M/°C) 0-100°C | Thermal Conductivity (W/M.K) At 100°C | Specific Heat 0-100°C (J/Kg.K) | Electrical Resistivity (NΩ.M) |
---|---|---|---|---|---|---|
430 | 7750 | 200 | 10.4 | 26.1 | 460 | 600 |
430 Stainless Steel Equivalent Grades
EU EN | USA UNS | Germany DIN,WNr | Japan JIS | China GB | Russia GOST |
---|---|---|---|---|---|
X6Cr17 | 430 S43000 | 1.4016 | SUS430 | 1Cr15 | 12KH17 |
Corrosion Resistance
All ferritic grades, such as stainless steel grade 430, have excellent stress corrosion cracking resistance. Grade 430 has good corrosion resistance to numerous substances, such as certain organic acids and nitric acid. The corrosion resistance is maximized in well-polished or buffed conditions. Its pitting and crevice corrosion resistance is quite similar to that of grade 304. 430F is a high-sulphur-free machining grade, and therefore the resistance to pitting and crevice corrosion is comparatively lesser than those grades that are non-free machining.
Welding
To perform any welding, stainless steel grade 430 has to be pre-heated at 150-200°C (302-392°F). In the case of embrittlement in the welded metal, the particular area can be post-weld annealed at 790-815°C (1454-1499°F); however, grain refinement will not happen.
It is recommended that grade 430, 308L, 309 or 310 filler rod should be used based on the application.
The ductility of the welded products can be improved by annealing post-welding at temperatures of 760 to 815°C. However, this is not required for thin welded products. Welding of exhaust tubing of automobiles is carried out without filler rods.
Heat Treatment
Solution annealing can be performed by heating stainless steel grade 430 to 815 – 845°C (1499-1553°F). Then it has to be slow furnace cooled to 600°C (1112°F) and followed by air-cooling quickly – as slow cooling between 540 and 400°C (1004 and 752°F) tends to cause embrittlement.
For sub-critical annealing, heating should be performed to 760-815°C (1400-1499°F), followed by air-cooling or water quenching.
This stainless steel cannot be hardened by thermal treatment.
430 Stainless Steel Applications
This grade of stainless steel can be supplied in all the usual forms: sheet, strip, plate, bar and tube. Its low cost combined with good corrosion resistance lends itself well to the making of domestic appliances. A lot of 430 stainless is used in cookers, washing machines, and dishwashers. Stove element supports are often produced in 430 stainless steel. It can also be found in shallow draw/limited-depth Stainless Steel sinks.
The motor industry uses a lot of 430 stainless steel in its automotive trim and muffler systems. You will also find it used for flue linings, industrial roofing, wall cladding, hinges, and fasteners.